Turbine Oil Filtration Plant CMM-1.2T
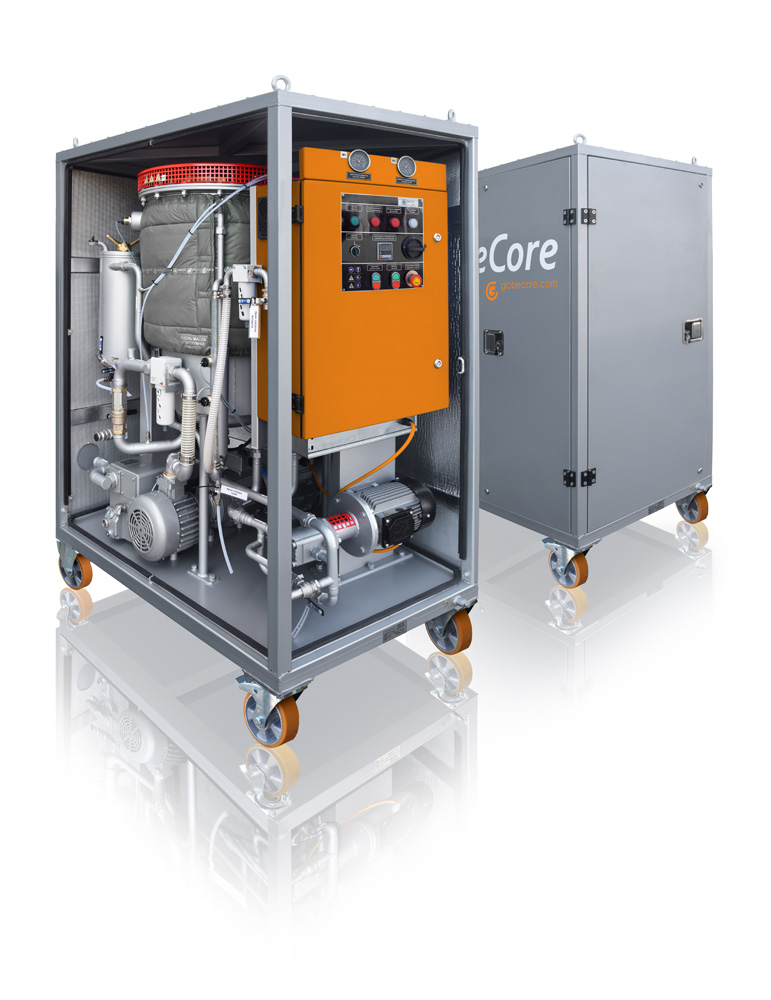
- Elimination of free and dissolved water
- Particles
- Carbon black
- Water soluble acids and alkalis
- Easy to operate and maintain
APPLICATION
CMM systems serve for inline dehydration and filtration of turbine oils for removal of free and soluble water and particulate matter. Most frequently encountered contaminants in turbine oil are water and solids. These contaminants are detrimental to the performance and life of the oil. CMM oil purification plant are fully acceptable for removing of these contaminations.
TECHNICAL PARAMETERS
Parameter |
Value |
|
1.Capacity, m3/h |
1.2 |
|
2. Parameters of treated oil | Filtration fineness, micron |
1 … 20 |
Humidity content, ppm |
10 |
|
3. Vacuum pressure, bar | Vacuum pump |
– 0.8 |
Vacuum vessel |
– 0.7 |
|
Inside the system, max |
8 |
|
4. Set power consumption, kW |
4.5 |
|
5*. Power supply, V, three phase, 50 Hz |
400 |
|
6. Dimensions, mm:- length- width- height |
1280 680 1230 |
|
7. Weight, kg |
370 |
*Power supply parameter as per clients’ requirement
WORKING PRINCIPLE
Input pump feeds the oil via mesh filter and cartridge filter into the vacuum column, through oil sprayer. In the vessel, the oil flows down the filling, which consists of polyplopylene rings. The rings are supported by a mesh above the bottom of the column. The flow is adjusted by input pump bypass line. The plant is operated from control cabinet.
Price:
The vacuum pump ejects the air from the upper part of the column. Air enters the column through a trottle valve in its lower part. When contaminated oil flows on the rings, it forms a very thin oil film with constantly changing surface. Vacuum lowers partial pressure of water in the oil and the water in free or emulsified state quickly evaporates. The moisture is separated in the moisture separator filter. Purified oil accumulates at the bottom of the vessel and is sucked out through the cartridge filter by the output pump.